Fuel Safety Research Group
Research on Fuel Behavior during RIA
An RIA is a power excursion accident that is caused by the ejection or dropping of a control rod (Fig. 4). The ejection of a control rod causes rapid increases in the power and temperature of adjacent fuel rods, and it may lead to failure of the adjacent fuel rods. We have conducted RIA simulation experiments by using the NSRR and investigated fuel failure conditions and fuel behavior during RIA.
At present, FSRG mainly investigates the failure conditions and mechanism of high-burnup fuels during RIA. At high burnup, the mechanical strength of the fuel cladding may be degraded by use for extended periods in the reactor. It is possible that the fuel fails because the degraded fuel cladding cannot resist the mechanical load applied by rapid thermal expansion of fuel pellets (Figs 3 and 5). This failure mode is called PCMI failure. Figure 6 summarizes the data obtained from the experiments conducted using high-burnup fuels. The obtained data and knowledge have been used for establishing safety regulations and procedures for safety review of high-burnup fuels.
Advanced use of the current types of LWRs, including further extension of fuel burnup, power uprating, and operation cycle extension, are promoted. We will continue to perform fuel safety research, including the behavior of advanced fuels during RIA.

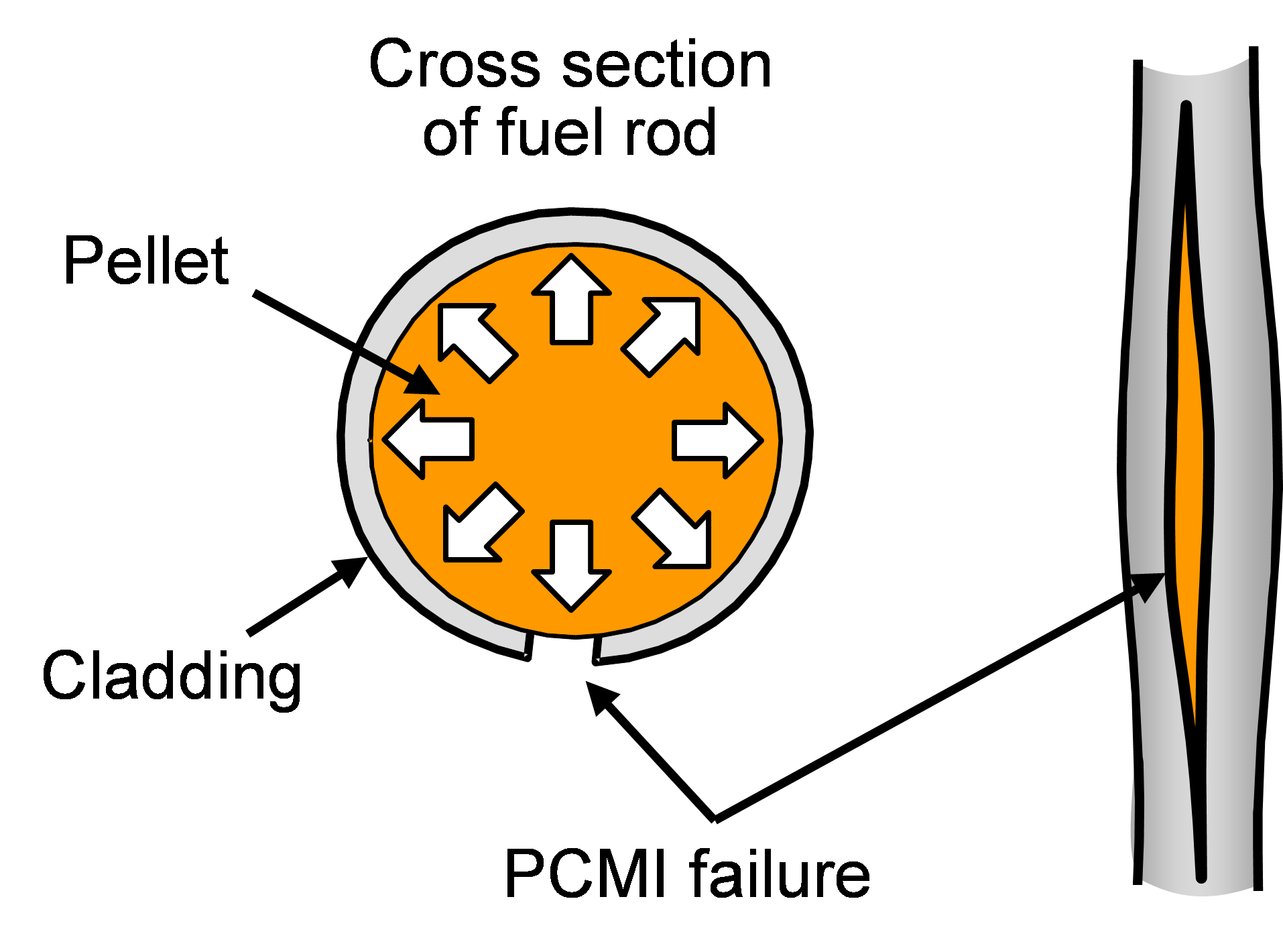
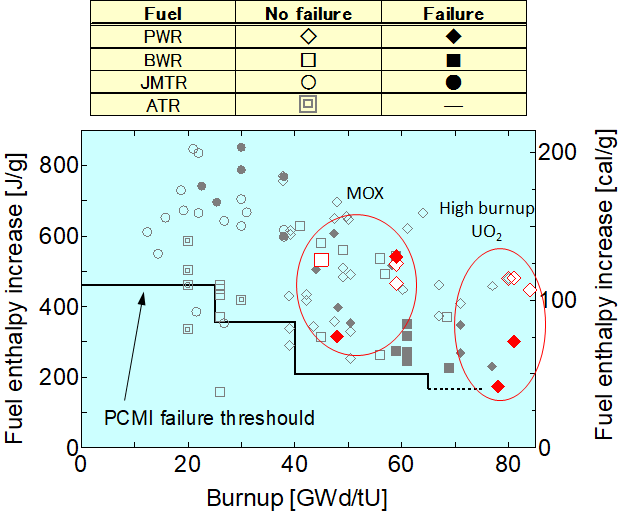
Fuel enthalpy is an index which corresponds to the loads generated thermally and mechanically in fuel rods during RIAs. The solid symbols show the increase in fuel enthalpy at failure, whereas the open symbols show the maximum increase in fuel enthalpy in the tests without failure. The solid symbols suggest that the increase in fuel enthalpy at failure decreases with increasing fuel burnup. The stepwise line in this figure is the PCMI failure threshold determined by the Nuclear Safety Commission of Japan. This threshold is used to judge the occurrence of PCMI failure under supposed RIA conditions in safety reviews. The data recently obtained (red symbols) show that the PCMI failure threshold is valid up to the burnup of approximately 80 MWd/kg, and it is applicable to MOX fuel rods.
Recent NSRR tests showed the lowest fuel failure enthalpy of an advanced fuel designed for Boiling Water Reactor (BWR) among the test results ever obtained at the NSRR in similar burnup range, and the rupture-type failure of high-burnup MOX fuel designed for Pressurized Water Reactor (PWR). Currently follow-up research activities are continued to identify reasons and/or underlying mechanisms of these new findings.
(The data were obtained under the research entrusted by Secretariat of Nuclear Regulation Authority.)
Research on Fuel Behavior during LOCA
Loss-of-coolant accidents (LOCAs) are caused by breaks in the primary cooling system or the like of reactors (Fig. 7). During a LOCA in an LWR, the coolant inventory would decrease or be lost in the reactor core, which results in fuel temperature increase due to the radioactive decay heat of fuels even though the reactor is shut down automatically. Even in such a case, the emergency core cooling system (ECCS) can eventually restore the water level in the reactor core so that the overheated fuels would be cooled down. However, if the cladding tubes are severely oxidized and embrittled before the ECCS is activated, the fuel rods may fracture due to the thermal shock caused by the ECCS cooling, resulting in the loss of a reactor core’s coolable geometry.
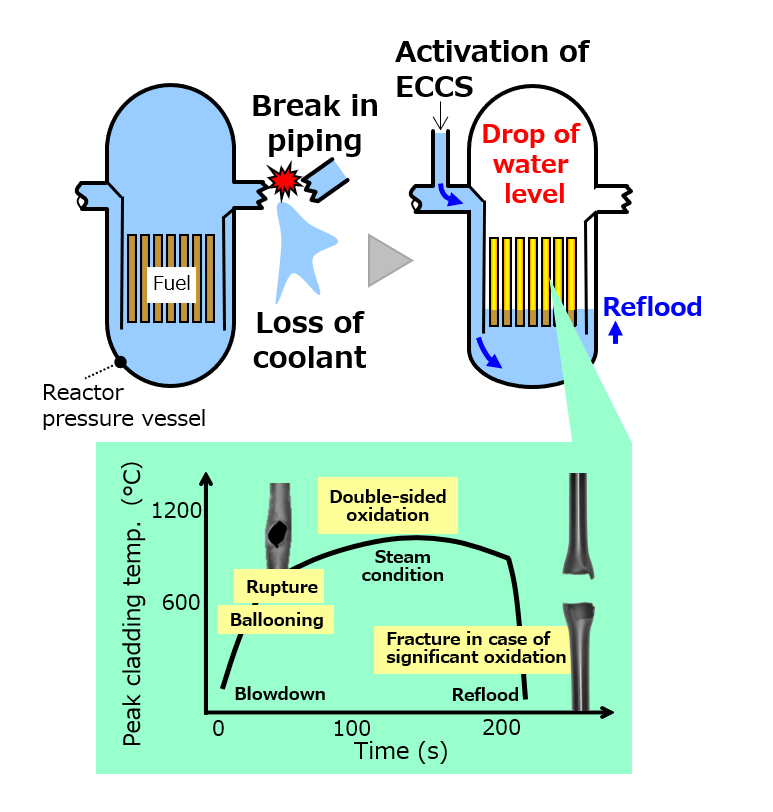
We investigate the fracture conditions of fuel cladding tubes in terms of the oxidation temperature and the amount of oxidation of cladding tubes performing LOCA-simulated experiments to contribute toward establishing regulatory criteria concerning the LOCAs. The ECCS acceptance criteria in Japan require that the peak cladding temperature should not exceed 1200°C and the amount of oxidation of cladding tube (the ratio of the thickness of the cladding tube metal layer reduced by oxidation to the thickness of the cladding tube metal layer before oxidation) should not exceed 15% to prevent the fuel rod fracture. These criteria were established in 1981 based mainly on results of LOCA-simulated experiments using unirradiated conventional fuel cladding tubes. Since the establishment of these criteria, the environment surrounding the fuel has changed, as represented by the increase in corrosion and hydrogen absorption of cladding tubes due to the fuel-burnup extension and the development of advanced fuel cladding tubes with high-corrosion resistance. However, the effect of these changes on the fracture conditions of fuel cladding tubes during LOCA was not clarified.
Therefore, we performed LOCA-simulated experiments using high-burnup advanced fuel cladding tubes to investigate the effect of the burnup extension and the use of advanced fuel cladding tubes on the fracture conditions of fuel cladding tubes under LOCA conditions (Fig. 8). In this figure, the open and the solid markers show the non-fracture and the fracture conditions of high-burnup advanced fuel cladding tubes during the LOCA-simulated experiments, respectively. The high-burnup advanced fuel cladding tubes did not fracture in the oxidation condition equal to or lower than the fracture limit of the unirradiated Zircaloy-4 cladding tube. Therefore, it can be concluded that the fracture limit of fuel cladding tubes is not significantly reduced by extending the burnup and using the advanced fuel cladding tubes, though it slightly decreases with increasing hydrogen absorption during normal reactor operation, and the current ECCS acceptance criteria in Japan are applicable to the high burnup advanced fuel cladding tubes.
(This study was performed under the research entrusted by Secretariat of Nuclear Regulation Authority.)
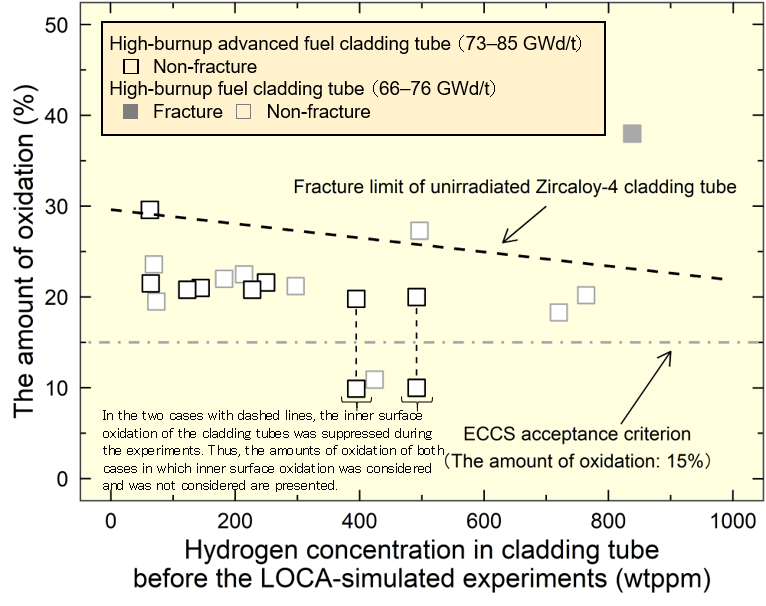
(Oxidation temperature during the LOCA-simulated experiments: 1200°C)
Development of Fuel Performance Codes
We have developed a fuel performance code RANNS to analyze mainly the fuel behavior during RIA. RANNS is used for analyzing a single fuel rod consisting of a pellet stack, cladding, and plenum. The analytical geometry of the fuel rod is shown in Fig. 9. The temperature, inner pressure change, and deformation (stress and strain) of the fuel rod can be calculated by coupling thermal and mechanical analyses. Analyses by using the RANNS code have clarified the thermal stress and the expansion induced in the fuel pellets, temperature change in the fuel rod, stress and strain induced in the cladding due to PCMI, and fuel failure condition during RIAs. To evaluate precisely the behavior of high-burnup fuel during RIA, it is also important to evaluate the fuel conditions at the onset of RIA events, which are an essential part of input data for accident analyses by the RANNS code. From this viewpoint, we have developed a fuel performance code FEMAXI-8 for analyzing fuel behavior under normal operation conditions. The initial release of FEMAXI-8 is available on the website of PRODAS.
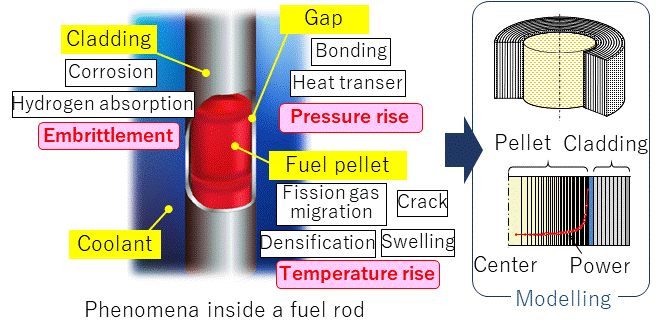