Criticality Safety Research Group
In Japan, there are various kinds of nuclear material, including spent nuclear fuel, that must be handled safely. Appropriate criticality safety control and attendant regulations are necessary to guarantee safety of workers and the public.
Reasonable safety margins will be taken into account by criticality analysis with less uncertainty, which makes the criticality safety control more effective. Introduction of “burn-up credit,” a typical example of such improvements, considers reactivity reduction by fuel burn. An essential study of criticality safety is necessary if the safety margin is not clear. A typical example is the criticality safety control of fuel debris resulting from the core-meltdown accident at Fukushima Daiichi Nuclear Power Station (1FNPS).
Our research subjects are:
(1) Establishment of the risk-assessment standard of fuel-debris criticality
The database designated “Criticality Map,” to be used to judge subcriticality of fuel debris taking fuel debris conditions as input parameters will be built using well-proven methods of modeling and computation.
(2) Verification of the “Criticality Map” by critical experiments
The criticality map will be validated by criticality experiments to enable judgments of shallow subcritical conditions of fuel debris. The Static Experiment Critical Facility (STACY) of the Japan Atomic Energy Agency (JAEA) will be converted to a general-purpose heterogeneous assembly built with fuel rods and water moderator that can produce various neutron spectra.
(3) Development of a criticality calculation method for the random material distribution in fuel debris
A new continuous-energy Monte Carlo solver "Solomon" is developed for analyzing uncertainty of criticality characteristics due to randomness of material distribution in fuel debris, consisting of fuels, concrete and structural materials.(Reference:)
(4) Post irradiation examination for validation of burnup calculation code and investigation for nuclide composition analysis of fuel debris
Post irradiation examination (PIE) of light water reactor fuels is carried out to validate burnup calculations for evaluation of nuclide composition of fuel debris. In addition, on the basis of this PIE technique, we are investigating an analysis method of actual fuel debris sampled in the future.
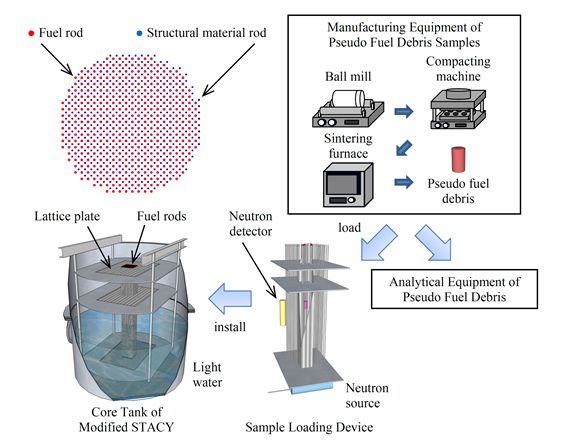