Materials Evaluation Research Group
Research on structural integrity of the reactor pressure vessels and core internals
More than half of the nuclear power plants (NPPs) in Japan have been operated for more than 30 years. For safe operations of such long-term operated NPPs, evaluating the effect of aging degradation on the structural integrity of nuclear components is critical. Our research aims to provide a technical regulatory basis (experimental or analytical data) for assessing aging management and approval for the lifetime extension of light water reactors (LWRs). To achieve our goal, we have been studying material degradations, such as irradiation embrittlement and stress corrosion cracking of reactor components in nuclear-specific environments, such as high temperature and neutron irradiation (Fig.1).
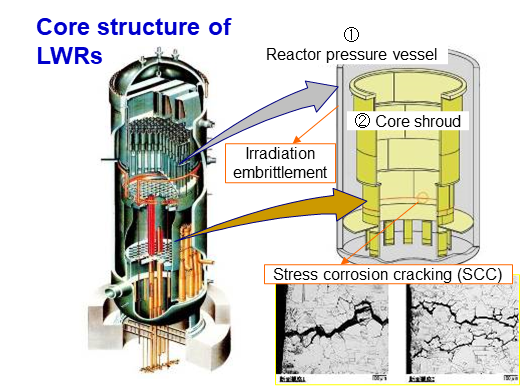
1. Irradiation embrittlement of reactor pressure vessels
The reactor pressure vessel (RPV, Fig. 1, labeled ①) is one of the most important safety-related structural components of nuclear reactors because it confines radioactive materials and coolant water. The RPV is made of low-alloy steel with a thickness of 150-200 mm. The low-alloy steel becomes brittle at low temperatures, and the embrittlement of steel progresses because of neutron irradiation from the core. Surveillance tests during plant operation monitor the irradiation embrittlement of RPV based on the reference temperature shift for nil-ductile transition (ΔRTNDT). Fig. 2 shows the resistance to fracture (fracture toughness) of RPV during an assessment period, estimated using the initial curve of fracture toughness and ΔRTNDT. However, a crack near the inner surface of RPV is postulated for assessing the structural integrity of RPV because of a pressurized thermal shock (PTS) event, which is the most severe event an RPV could experience. The change in the stress intensity factor (a parameter representing the driving force for crack initiation) at the crack tip is evaluated (the blue curve in Fig. 2). The assessment confirms the safety margin between the fracture toughness and stress intensity factor.
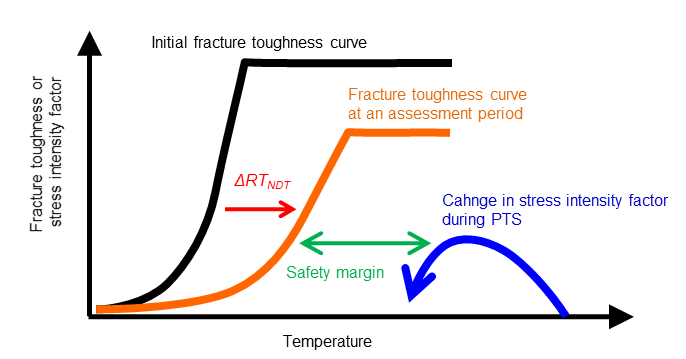
1.1 Study on fracture toughness evaluation
In the surveillance test, the fracture toughness of irradiated RPV steels is determined based on the Charpy impact test. Recently, fracture toughness tests using 0.16T-C(T) (Mini-C(T)) specimens were developed and used in the standard test method for determining the reference temperature, To (a parameter representing the ductile-brittle transition temperature region of ferritic steels). We investigated the applicability of Mini-C(T) specimens for fracture toughness evaluation of unirradiated and irradiated RPV steels by comparing To obtained from Mini-C(T) specimens to that obtained from larger specimens such as 1T-C(T) specimens (Fig.3).
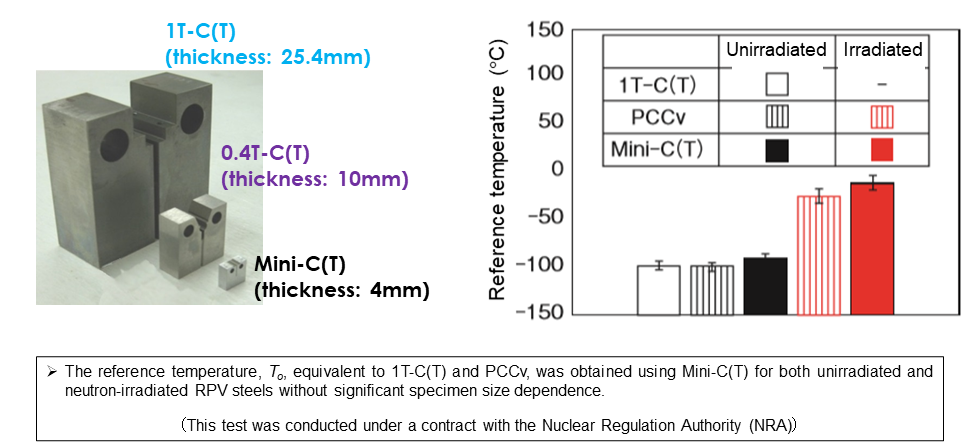
1.2 Microstructure analysis for irradiated RPV steels
The irradiation embrittlement prediction is critical for the structural integrity assessment of RPV. Microstructural changes such as the clustering of solute atoms and formation of dislocation loops predominantly cause irradiation hardening and embrittlement. The irradiation embrittlement prediction is improved by investigating the embrittlement mechanism correlated with the microstructural changes. The microstructural changes of RPV steels due to irradiation might depend on the initial conditions of material, such as chemical composition and inhomogeneous phases produced by fabrication processes, including welding and heat treatment. We have observed the microstructural changes using electron backscatter diffraction analysis on scanning electron microscopy (SEM-EBSD), three-dimensional atom probe tomography and transmission electron microscopy (TEM). Currently, we are focusing on the irradiation embrittlement of the heat-affected zone in RPV steels (Fig.4).
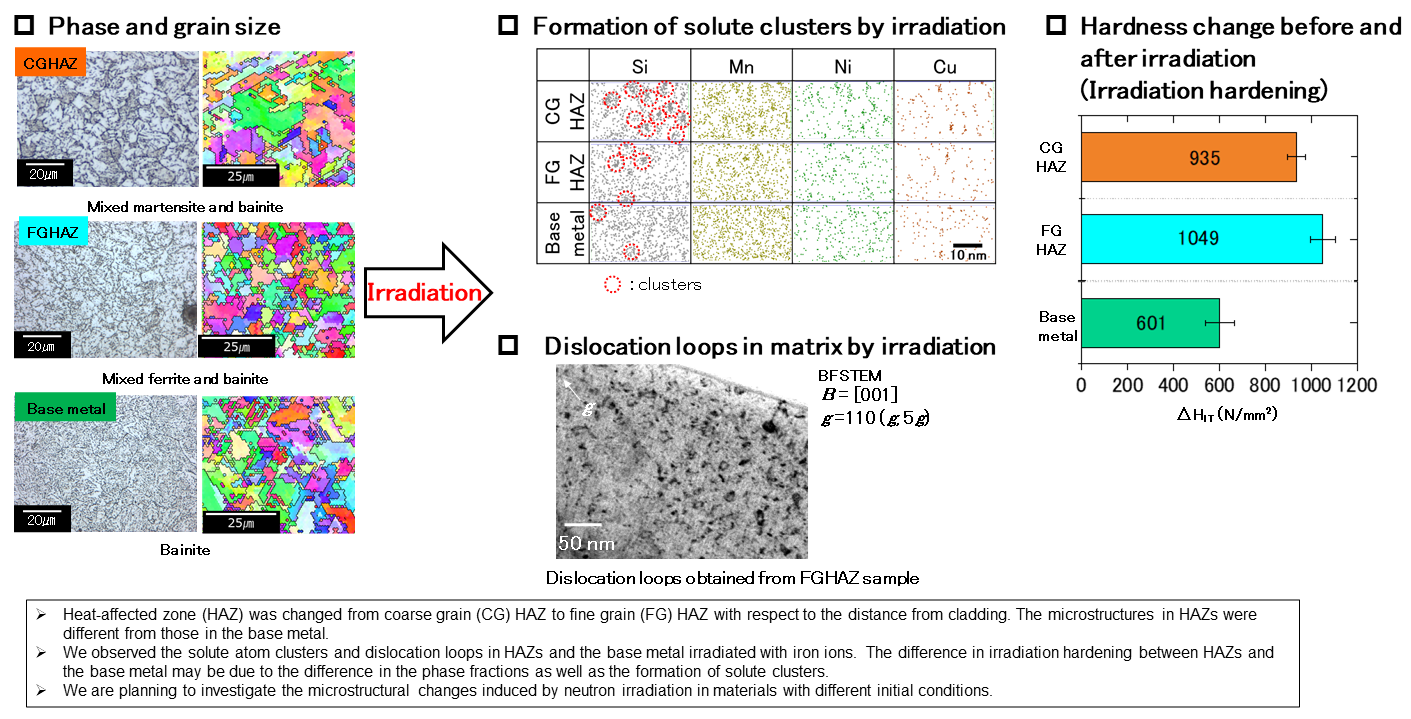
1.3 Bayesian statistical analysis for irradiation embrittlement in RPV steels
We investigated influential parameters for irradiation embrittlement by developing a machine-learning technique based on the Bayesian nonparametric (BNP) method, which considers the number of periphery data and scatter. By using this technique, the effects of neutron irradiation conditions and chemical compositions on irradiation embrittlement have been studied for Japanese surveillance data (Fig.5).
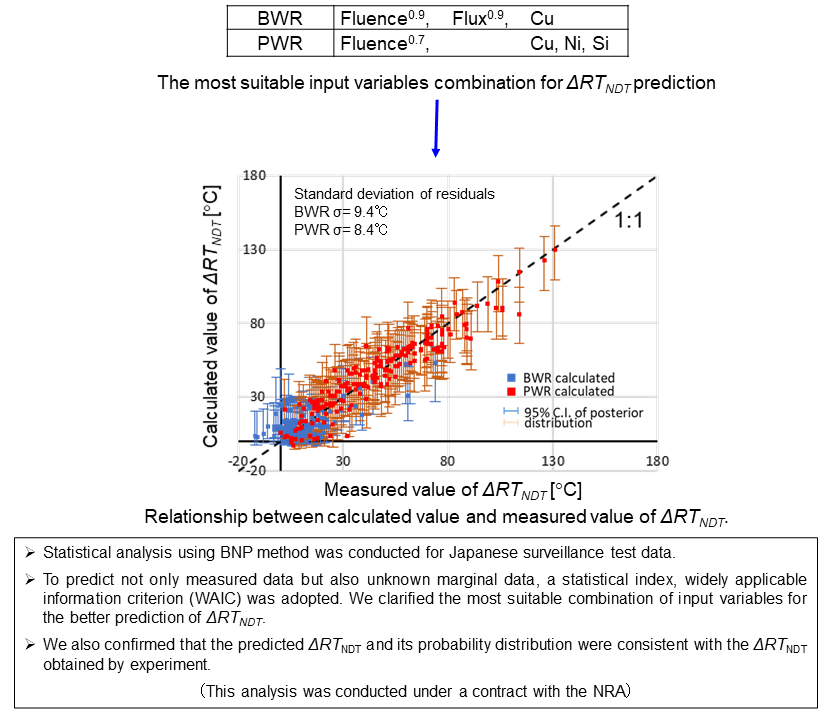
1.4 Finite element analysis for fracture mechanics evaluation
In the current Japanese structural integrity assessment for the RPV, an under-clad crack (UCC) is postulated near the inner surface. We estimated the effect of cladding on the fracture toughness of the RPV by conducting fracture toughness tests for the specimen with an UCC and finite element analyses (FEAs) for investigating the plastic constraint at the crack tip of the UCC (Fig.6).
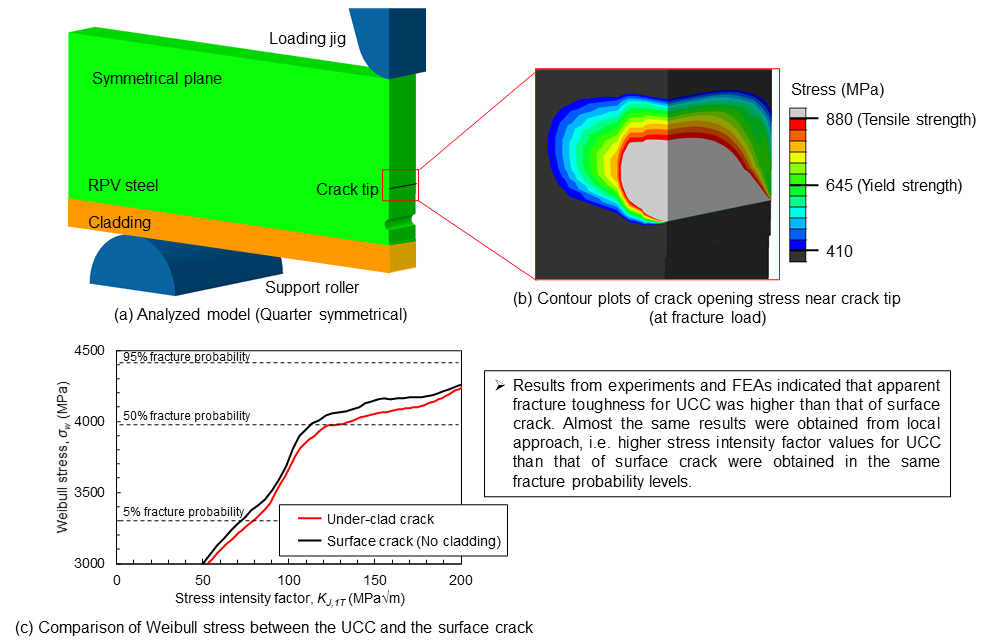
2. Stress corrosion cracking of reactor core internals
In the structural integrity evaluation of stress corrosion cracking (SCC) of stainless steel components used in reactor core internals, such as a core shroud (Fig. 1, labeled ②) of a boiling water reactor (BWR), it is important to understand the effects of stress, material properties, and environmental conditions, such as water chemistry, on SCC, and improve the evaluation method for proper inspection, repair, and replacement of the components. In this study, we performed crack growth rate tests for stainless steels under simulated LWR conditions to improve the evaluation method and investigate the effects of water chemistry and irradiation conditions on the crack growth rate because of SCC. We also obtained data on the deformation and corrosion (oxidation) of stainless steels to understand the SCC phenomena through mechanistic investigation (Fig.7).
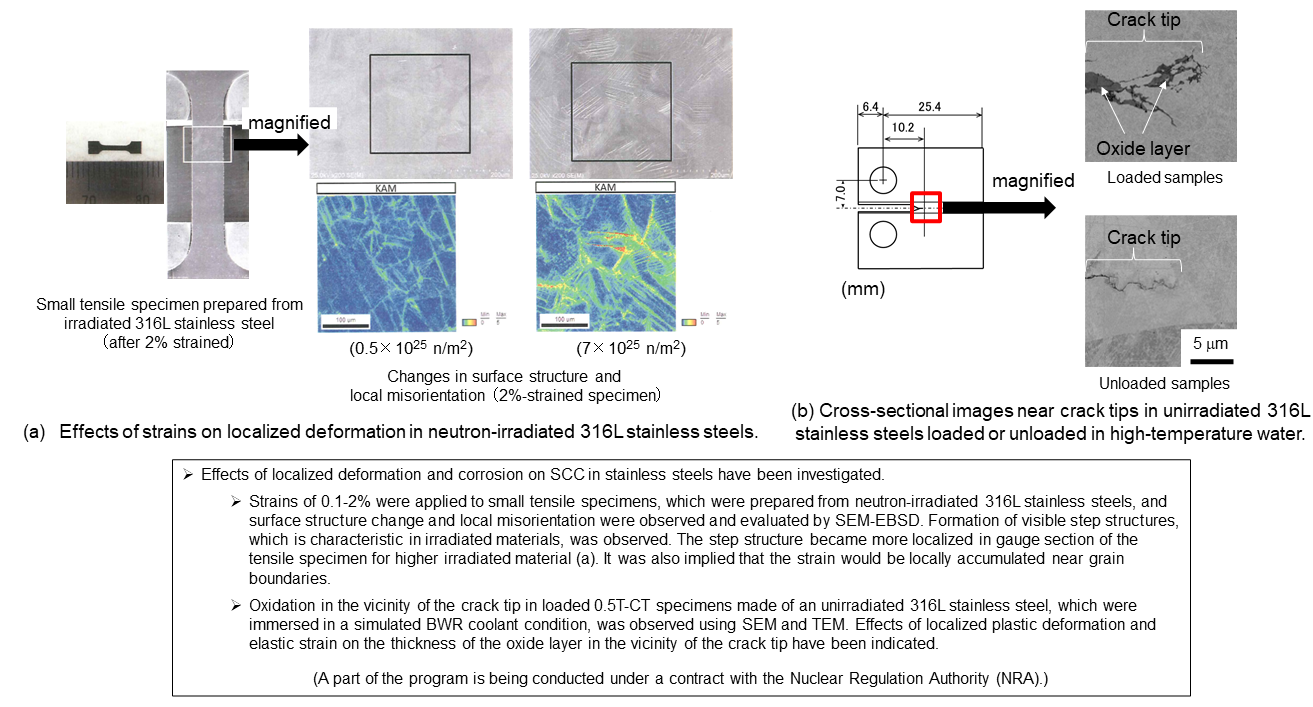