
Visualization of bubble collapse process in liquid metal and development of surface improvement technology
May. 15, 2007
POINT : Bubble formation and collapse behavior in liquid mercury, which will be cased by pressure waves propagation in mercury targets for pulsed spallation neutron sources, were visualized and a novel surface improvement technology was developed based on the visualization. The surface improvement technology will be applicable for components of automobiles, industrial machines, nuclear structures, etc.
OUTLINE : R&D on mercury targets for pulse spallation neutron sources, which will be able to produce neutron beams with intensity 6 times higher than that produced by the present facility, is carried out in J-PARC [ Director Shoji Nagamiya], jointly constructed by two national agencies, Japan Atomic Energy Agency (JAEA [President Toshio Okazaki]) and High Energy Accelerator Research Organization (KEK [Director General Atsuto Suzuki ].
High intense proton beams will be injected into mercury target to induce the spallation reaction. At the moment the intense proton beam hits the target, pressure waves are generated in the mercury because of the abrupt heat deposition. The pressure waves interact with the target vessel leading to negative pressure that may cause cavitation along the vessel wall. Localized impacts by micro-jets and /or shock waves which are caused by cavitation bubble collapse impose pitting damage on the vessel wall. The pitting damage which degrades the structural integrity of target vessels is a crucial issue for high power mercury targets.
The visualization of mercury cavitation-bubble collapse behaviour was carried out by using a high-speed video camera (Shimadzu HPV-1). In the experiment, the pressure wave was generated in mercury by using electric magnetic force instead of proton beam injection because of avoiding radiation hazard. The micro-jet and shock waves were clearly observed at the mercury micro-bubble collapse as shown in Fig.1. Localized impact was quantitatively estimated through comparison between experiment and numerical simulation in which the micro-jet was simulated by droplet collision against solid wall. Localized impact was quantitatively estimated through comparison between numerical simulation and experiment.
A novel surface treatment technique that consists of plasma carburizing and nitriding processes was developed. The treatment condition was optimized to achieve an improved surface layer with a suitable hardness gradient that can mitigate the pitting damage due to localized impacts, taking into account the stress distribution evaluated quantitatively by micro-jet impact simulation based on the visualization. The surface improvement is effective to increase the lifetime of mercury target vessel.
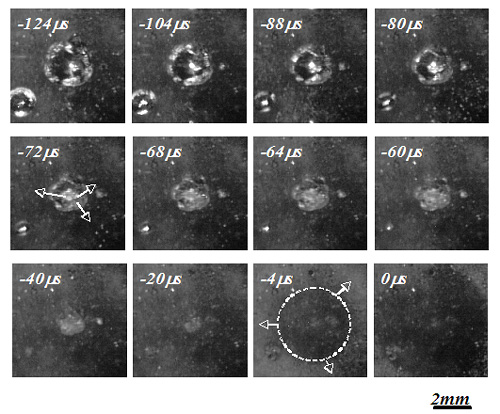
Figure 1 Collapse behavior of mercury cavitation bubble with micro-jet injection. It was observed that the micro-jet was injected to the glass wall from -72 μs to -40 μs during bubble collapsing. The mist was brought about at -4 μs after completely bubble collapse and radiated circumferentially at 0 μs.
|

Location of environment monitoring posts measuring amount of
radiation. (details)

International link directory of related websites.
|